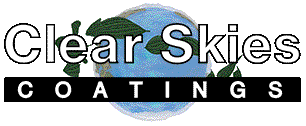
Ad-Pro Zero® Presentation
What I am going to present today is a revolutionary adhesion promoter for TPO that is high performance and yet has zero Volatile Organic Compounds (VOC’s), zero Hazardous Air Pollutants (HAP’s), and it’s halogen-free. It’s a powder coating, but it’s one which we have converted into a colloidal suspension of powder coating particles in water. This combination of powder and liquid technologies gives the user all the application benefits of a liquid coating with all the performance and environmental benefits of a powder coating.
Now, as we all know, TPO is not readily paintable. It requires a flame or plasma surface treatment widely used in Europe or a spray applied adhesion promoter widely used in the Americas and Asia. As pointed out in Ryntz and Yaneff in Coatings of Polymers and Plastics, “Using an adhesion promoter is probably the most effective, most robust, and most versatile process but also the most expensive and environmentally unfriendly.” Ulrich Poth in Automotive Coatings Formulation points out that “Many trials have been designed to replace solvent-borne adhesion promoters with more environmentally friendly products, but the perfect solution is still to be found.”
Conventional liquid adhesion promoters contain a blend of standard paint resins and crosslinkers as well as a modified polyolefin resin, modified with either chlorine or maleic anhydride. The modified polyolefin resin is the secret sauce that provides adhesion to TPO.
The first challenge the ad-pro formulator faces is lack of compatibility between the polyolefin resin, the secret sauce, and the co-resin. Polyolefin resins dissolve nicely in hydrocarbon solvents like toluene, while standard paint resins (co-resins) usually dissolve nicely in oxygenated solvents like normal butyl acetate. But now when you try to combine these two solutions they do not like one another. They will phase out into two separate layers like oil and vinegar. Now, there are hundreds of formulas for TPO ad-pro and in each case the formulator needed to find a resolution to the incompatibility issue and in each case they did. But, in so doing they made some compromises. They probably chose to use chlorine modified polyolefin resin instead of the more environmentally friendly maleic anhydride type, because the chlorine type has better compatibility with co-resins. They may have chosen to use lower molecular weight polyolefin resins, because they take less solvent to dissolve them versus higher molecular weight ones which give better gasoline and chemical resistance.
We have discovered a totally different method of addressing the issue of incompatibility. For this discovery we were awarded a patent. You can see it is very recent with a publication date of June 3rd of this year.
But, bare TPO is a non-conductive surface so watch what happens when we try to powder coat bare TPO with our adhesion promoter, while it is still in a conventional powder form. The panel on the left in this short video is a steel test panel and the panel on the right is a bare TPO test panel. Oops! We have a problem. Unless we have a conductive surface with a continuous path to ground we get zero transfer efficiency and of course TPO is non-conductive. Another problem is that powders are applied to a dry film thicknesses of about 70 microns. The electro-static application of a powder coating builds film thickness so quickly it is impossible to get a consistent film build of less than about 25 microns. And ad-pro should be applied in a very thin coat about 3 to 5 microns. Unless we can resolve the application issues the whole idea has no commercial value. So, we convert the conventional powder coating into a colloidal suspension of powder coating particles in water.
Conventional powder coatings contain solid particles of paint usually around 25 microns in diameter that are separated from one another by air. We replace the air with water and further reduce the particle size down to about 5 microns. At 5 microns particle size we can have a stable colloidal suspension. Here is a short video showing our liquid powder slurry ad-pro being applied to a TPO test panel using a high volume low pressure spray gun.
Note that the color is a medium gray but we have still have made it conductive so that subsequent layers of base coat and clear coat can be applied electrostatically by rotary spray equipment or anything else. The simple and inexpensive way to make a coating conductive is to use conductive grade of carbon black pigment loaded at about 1 to 2 percent. But, by the time you have reached a percolation point for conductivity you are stuck with a black color, not exactly ideal for use over a black substrate considering how critical it is to get ad-pro on the part. Fascias that do not get ad-pro for some reason will have catastrophic loss of adhesion – like this part here, or this one, or this one or, less dramatically like this one or this one. So, we took the couple dollars per gallon we saved by removing the toluene and other solvents and re-invested it in a different kind of conductive material. We use Single Walled Carbon Nano-Tubes to get the conductivity. Now, these have been around for several years, but were prohibitively expensive. They’re still very expensive, but we use them at a very low percentage.
In principle this adhesion promoter works in a manner similar to all the hundreds of ad-pro formulas prior to this, except without any of the health, safety, or environmental issues. Coatings adhere to substrates through combination of mechanical and chemical means. Polyolefin, like TPO and polypropylene, are difficult to adhere to, because they are non-polar materials. They are solid hydrocarbons having no elements other than carbon and hydrogen in the polymer. Without any heteroatoms in the polymer such as nitrogen, or chlorine, or oxyge (especially oxygen) bonding to such a surface is difficult. This is because paint generally adheres to a substrate primarily through the attractive forces of polar groups in the paint resin with polar groups in the substrate rather than developing any true covalent bonds between the coating and the substrate. These attractive forces are known as Van der Walls attractive forces and they’re fairly week, on the order of 8 kJ/ mole versus 100 kJ/mole for a covalent bond. But we can have trillions and trillions of these Van der Walls attractive forces between a coating and a substrate and it’s enough to give us excellent adhesion. So, (and this is the critical part about why it’s so hard to paint TPO) how does an adhesion promoter adhere to TPO if TPO only has carbon and hydrogen and the carbon-hydrogen bonds in TPO are non-polar? Polyolefin hydrocarbon resins have a special capability that standard paint resins do not have. They can diffuse into TPO and become entangled in the hydrocarbon polymers of the TPO. We call this molecular diffusion and entanglement. In this slide you can see where I’ve shown an idealized TPO surface on the bottom and also the polyolefin resin above it – in this case a chlorine modified polyolefin resin. Here is the maleic anhydride modified version . There is a lot of jiggling and wiggling, twisting and bending of the polymer chains in both the substrate and the coating so that the polyolefin resin in the ad-pro can diffuse its way into the top layer of the TPO and get trapped there.
We think the after-market fascia business might be the best place to introduce our patented Ad-Pro Zero. Molding and painting TPO fascias is done by just a couple of suppliers in large plants producing about 3,000,000 fascias per year with about 20% of them for the after-market. Typically they have separate paint lines for after-market parts and OE parts. The after-market parts get a thin coat of ad-pro followed by a primer coat. The OE parts get a coat of ad-pro followed directly by base color and clear without a primer. The only purpose of the primer on the after-market parts is to protect them during shipment anda lengthy storage before the get used by a collision repair shop. For after-market fascias this powder slurry can be used as an ad-pro at about 3 to 5 microns or perhaps as a sandable ad-pro / primer at 8 microns, because ad-pro slurry is much tougher than any liquid ad-pro. Of course it’s tougher, it’s a powder coating.
Fascia suppliers, like automotive assembly plants, are tightly regulated for paint shop emissions. They’re required to “burn off’” the solvent vapors before exhausting spray booth air and oven air to the atmosphere. This is done in a Regenerative Thermal Oxidizer that operate at about 1,350°F. A garden variety RTO unit will cost around $60,000,000 to install and will use about $1,000,000 of natural gas per year to maintain the operating temperature. RTO’s are still the center-piece of the EPA’s strategy to limit VOC emissions from large paint shops, even though they emit 10 lbs. of global warming carbon dioxide for every 1 lb. of smog producing VOC’s burned off. Now, they were first mandated by the EPA in the late 1970’s. I started my career in the coatings business in 1977 as a materials engineer in the paint lab at Chrysler. Back in 1977 we had no internet, no personal computers, no mobile phones, we also had no flexible plastic fascias for cars at Chrysler. Cars, like trucks, still had chrome-plated steel bumpers. RIM urethane fascias molded and painted by Davidson Rubber Company started to show-up upon Chrysler vehicles in about 1980. But, do you know what else we did not have much of? We did not have much of an understanding of the role carbon dioxide played in the atmosphere as a greenhouse gas. We knew exactly what VOC’s did in the atmosphere that they underwent photo degradation and produced low level ozone, the primary constituent of urban smog. In 1977 we thought carbon dioxide was just a simple inorganic compound which was absolutely essential for plant growth. So, mandating the use of an RTO which generates a bunch of greenhouse gases to burn off VOC’s made sense. But soon RTO’s will be recognized for what they really are “pollution generating devices” not “pollution control devices”. No one will ever be successful by going to the regulatory agencies with a story of reduced VOC’s and asking for authorization to turn off their RTO. You will need to get to zero VOC’s and zero HAP’s to turn off the RTO’s. We believe we can do this right now for the after-market fascias as a first step in commercializing our patented Ad-Pro Zero.
Here is my contact information.
We are ready to supply samples, conduct trials, and work through the approval processes to use our zero VOC, zero HAPS, halogen-free Ad-Pro Zero for any automotive or non-automotive low surface energy substrate that needs to be painted.